Climate and carbon: concrete benefits of timber
Why would someone who “blooming loves concrete” choose a timber frame for his latest house? As Adrian explains, it’s all about climate and carbon.
Hill Top House
12 years ago I designed a house called Hill Top whose structure and interior were entirely precast concrete. Flatpack concrete panels were assembled like a pack of cards in a few days; the interior was self-finished, extremely durable and a thing of austere Ando-esque beauty. It felt like the future for building technology. It also felt timeless and resonant; to go through the front door was to immerse in an ascetic poem. Boy it was special; and it was recognised as such. It won an RIBA Award. And despite being the smallest entrant by a mile it beat the Goliaths to win the Concrete Society award for the best concrete building in the UK that year.
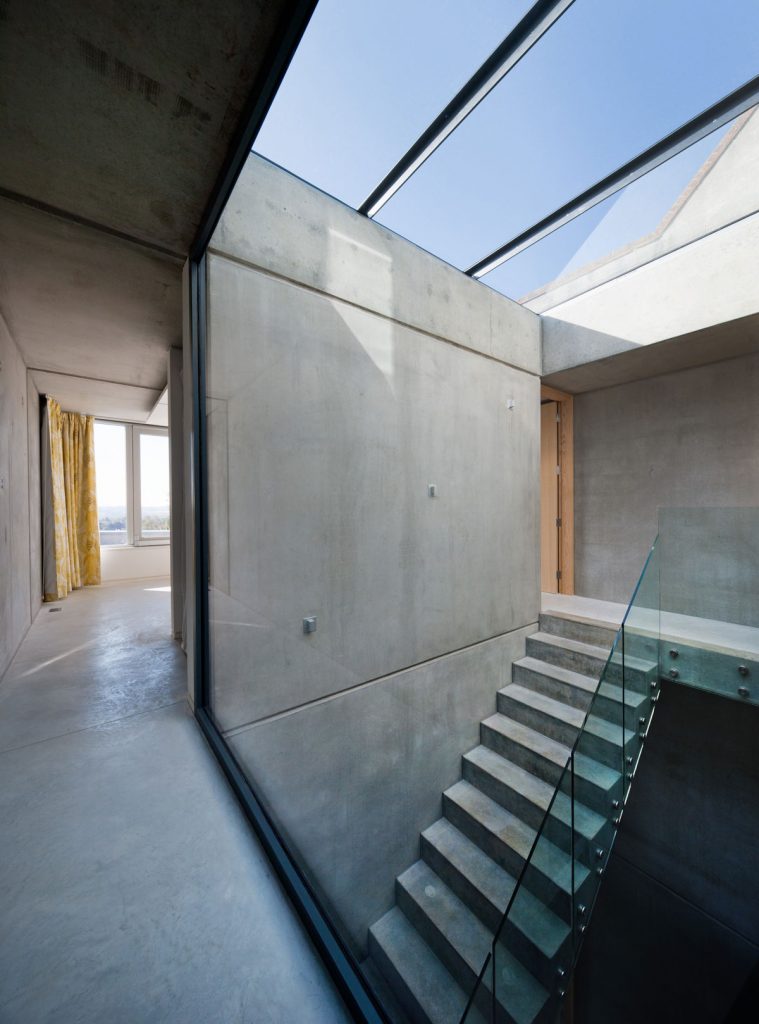
It was also a dream come true for me as an ardent advocate for concrete. I had written an encomium to the material in Concrete Quarterly (still my favourite journal) a decade earlier. So when I came to design our new family home my instinct was to once again use concrete to its utmost. My wife and I paid a pilgrimage to Hill Top to see how it had fared over the intervening years. It was a joy. The concrete had aged minimally. There was a sheen in those areas frequently touched and there was a subtle patination to the floor of the kitchen as testimony to the owners’ lives well lived. And yes, there was still that majestic aura of mass and truth.
The elephant in the room
But as we now well know, there is an elephant in the concrete room and it has a very large carbon footprint. I do not agree with those who advocate that concrete must go. It is the most versatile and useful building material on earth. It is the opposite of plasterboard which makes every building a cheap stage set; it is hard reality. And actually it need not be such a carbon bogeyman.
Concrete, after all, is nine-tenths inert rock and sand, stuff which can be sourced locally and lasts forever with no carbon impact. Concrete is basically glued gravel, and it is only the glue that is the problem. The cement. The industry is acutely aware of this issue and is investing hugely to decarbonise cement and/or find alternative glues. It would be nice to think that in ten years’ time the cement conundrum will be solved and concrete will revert to being the world’s greatest building material.
Right now, it’s not there. And there is an additional problem when designing a house rather than a megastructure. Concrete is just too damn good at what it does; a two storey house made of concrete is inevitably over-engineered. It does not need such strength or such mass. Yes, thermal mass is very important but it can just be a ground floor slab or a stone wall or two. Less is more, and with the climate crisis galloping towards us, less is a must.
Moving to timber
So we have foregone concrete for the structure of Copper Bottom. We first used SIPs for another house we built 8 years ago called Sandpath. (This one also bagged an RIBA Award, and was feted as the Best House of the Year at the British Home Awards.) At the time the reduction in the embodied energy in the house was not the driver for using SIPs; it was all about U-values and airtightness plus off-site efficiency, quality, safety and speed. Today the carbon embedded in the timber really matters too, and SIPs feel right on all counts.
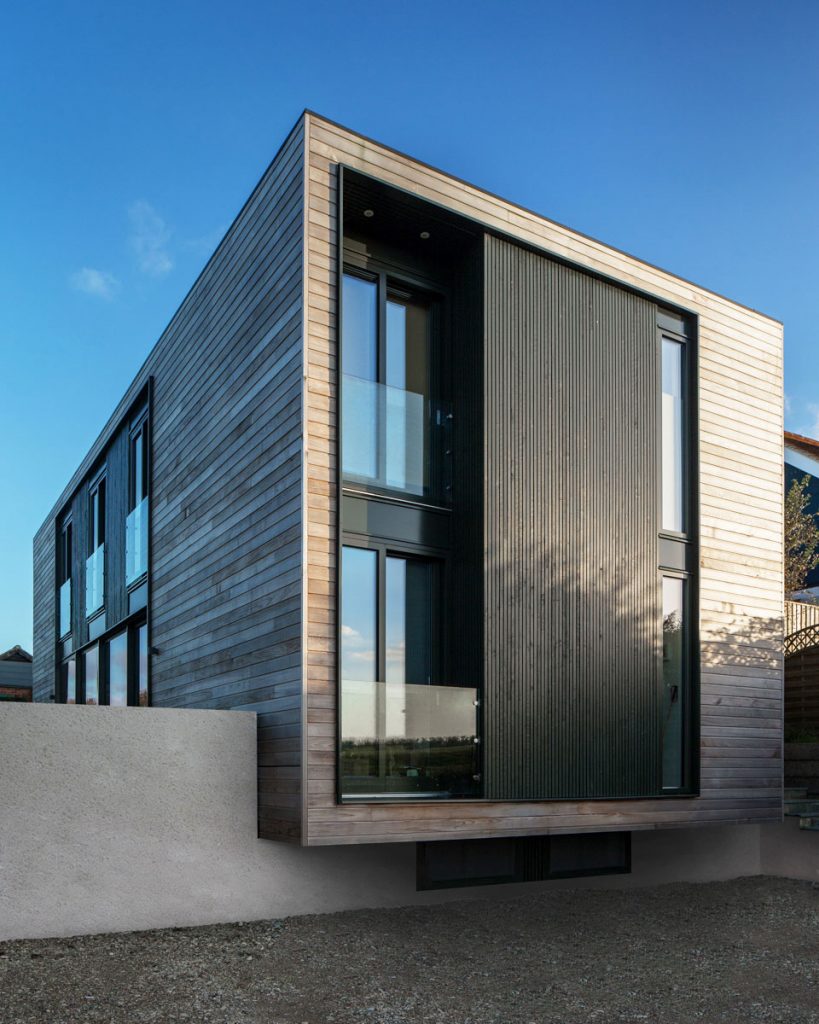
The end result
End result: Copper Bottom is being assembled like a pack of cards in a few days just as Hill Top was. But the cards are now prefabricated structural insulated panels. Wide softwood studs are assembled into cassettes packed with insulation and faced in OSB. These create an envelope with the requisite U-value and airtightness to meet Passivhaus standards. I still blooming love concrete, but I also love timber for all its manifest qualities, and that is what we are using here.